
.jpg)
While collaborative robots still make up just a small part of all robots, their share is expected to continue growing at least until 2022.
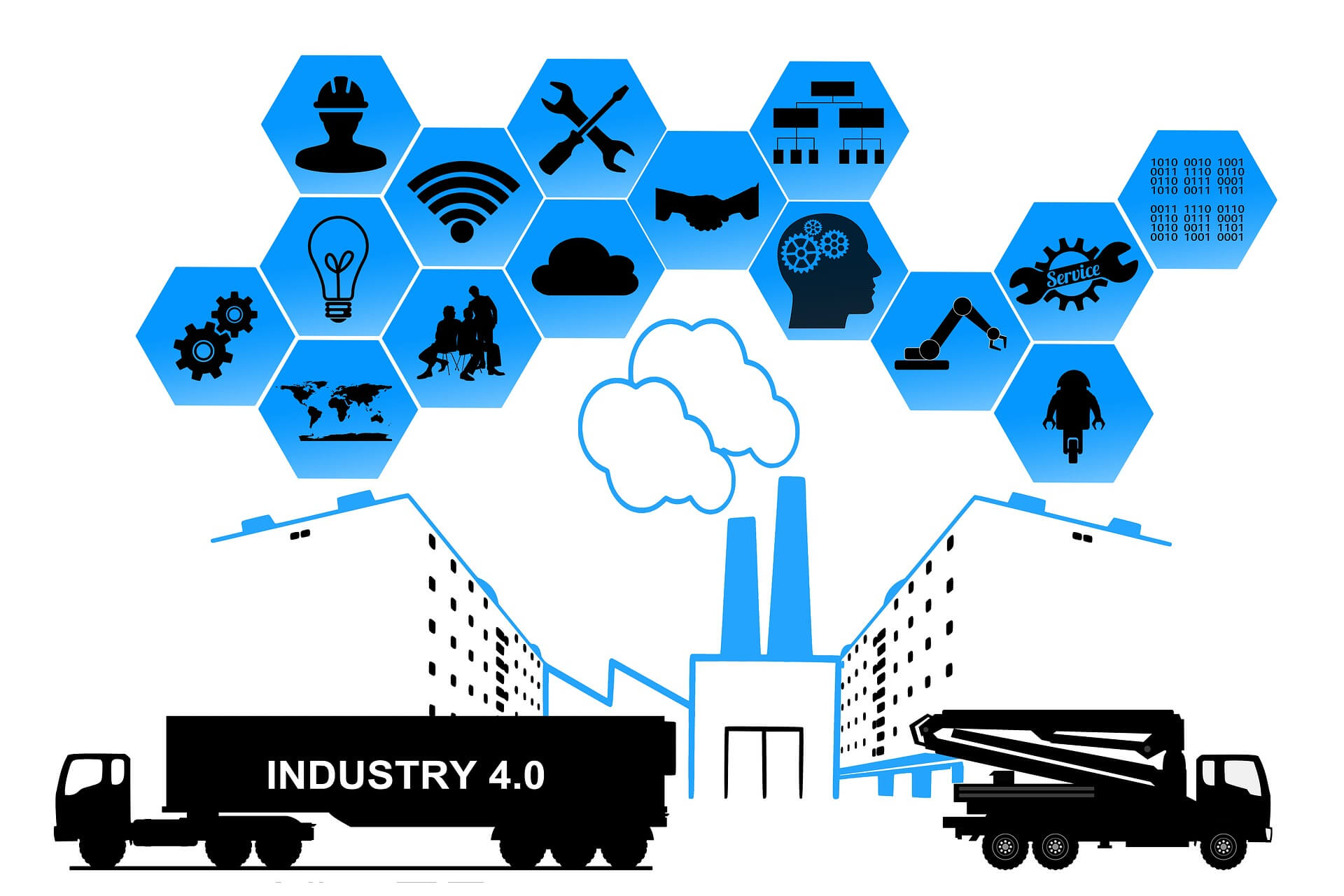
The way forward might thus be combining robots and humans’ strengths and creating workspaces where they can collaborate. Although robots’ capabilities are increasing, they still cannot do everything humans can. The top three countries with the most robots per 10,000 employees in the manufacturing industry – Singapore, South Korea, and Japan – have one of the lowest unemployment rates in the APAC region. While it is true that some low-skilled workers will lose their jobs to robots, the introduction of robots can lead to the creation of new jobs. Understandably, they fear being replaced by robots. Using historical data, intelligent automation can analyze past and. From simple tasks to assembly and inspection processes. Not all workers appreciate the rising number of robots in workplaces, though. The explosive growth of automation has revolutionized the manufacturing industry. Automation has become an unavoidable trend for achieving low costs and high quality in manufacturing. The tasks that robots do tend to be dull, dirty, dangerous, or difficult (collectively called the 4 Ds of robotization) and thus better suited for machines. The machines can be simple, such as computer numerical control (CNC) machines or palletizers designed to do a specific task, or more complicated, such as robots that can be programmed to carry out different tasks. In an automated manufacturing facility, it is machines that carry out tasks formerly performed by human workers. Robots as an option to automate physical tasks This made automotive factories much safer for their employees. However, they were still able to perform basic tasks like pick and place. Early industrial robots had no external sensors. In 1970, when the first integrated circuit appeared, the automation race was on. Once the devices are connected, they can be monitored and controlled as a system, and the data the devices retrieve can be collected and analyzed at the edge of the network or in the cloud, allowing for improving the efficiency of production and maintenance. The conflict accelerated development of technologies like the first computer.
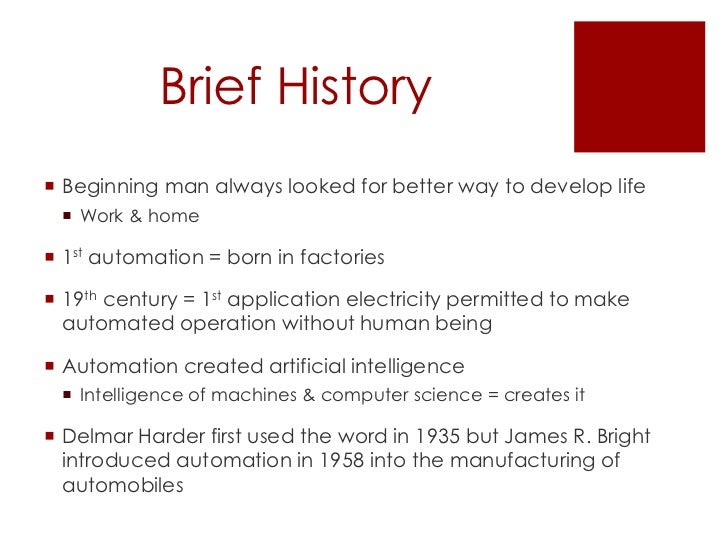
On the other hand, there needs to be an infrastructure alongside solutions enabling all these devices to connect to and communicate with each other (also called the Industrial Internet of Things). On the one hand, there are technologies that allow the design and manufacturing of a product with the help of a computer and machines that take part in manufacturing, assembling, and packaging of the product. Industrial automation comprises a range of technologies that complement each other.
